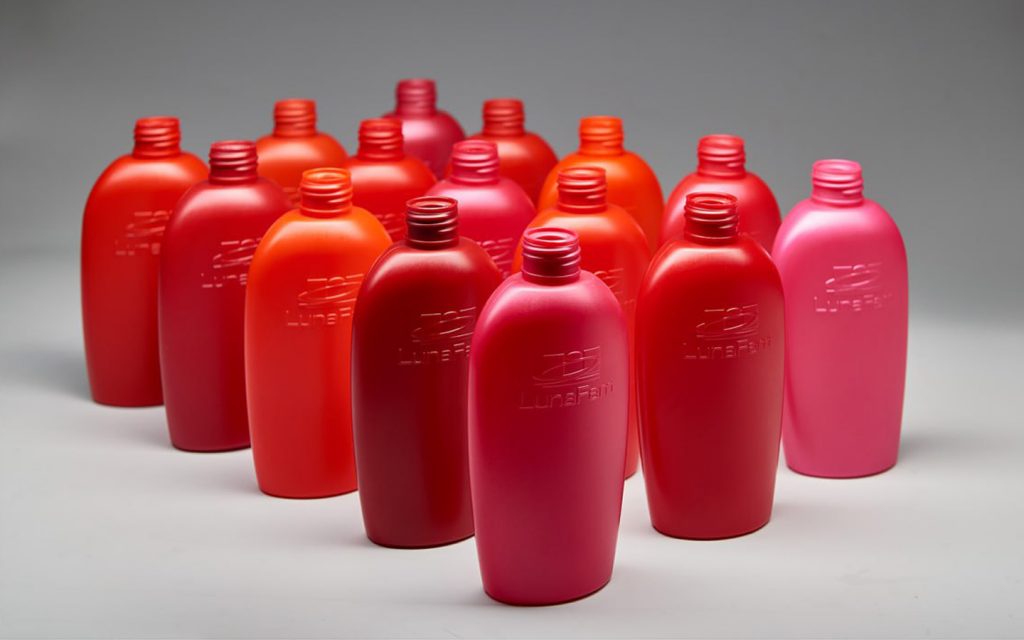
PP/PE Bottles
Blow molding is a manufacturing process used to create hollow plastic products, such as bottles and containers, by inflating a heated plastic tube (parison) inside a mold. PP (Polypropylene) and PE (Polyethylene) are two common thermoplastics used in this process due to their excellent molding properties and durability.
Characteristics
1. Polypropylene (PP) Bottles
Higher Heat Resistance – Can withstand temperatures up to 100-120°C without deforming.
Stiff and Rigid – More rigid than PE, making it ideal for containers requiring structural integrity.
Chemical Resistance – Resistant to many acids, bases, and organic solvents.
Transparent or Opaque – Can be made semi-transparent but is usually more opaque than PET.
Low Density – Lighter than many plastics, making it cost-effective for transport.
Applications of PP Bottles:
- Pharmaceutical bottles (medicine syrups, eye drops)
- Hot-fill bottles for food and beverages
- Cosmetic containers (shampoos, lotions)
- Chemical packaging (household cleaners, detergents)
2. Polyethylene (PE) Bottles
There are two main types of PE used in blow molding: HDPE (High-Density Polyethylene) and LDPE (Low-Density Polyethylene).
Impact Resistance – PE bottles are flexible and resistant to cracking.
Excellent Moisture Barrier – Ideal for liquid storage.
Chemical Resistance – Suitable for storing detergents, oils, and mild chemicals.
Translucent Appearance – HDPE bottles are typically opaque, while LDPE bottles are more flexible and semi-transparent.
Good Low-Temperature Performance – Can be used in cold environments without becoming brittle.
Applications of PE Bottles:
- HDPE: Milk jugs, motor oil bottles, shampoo bottles, detergent containers.
- LDPE: Squeeze bottles (honey, sauces), flexible packaging for cosmetics.