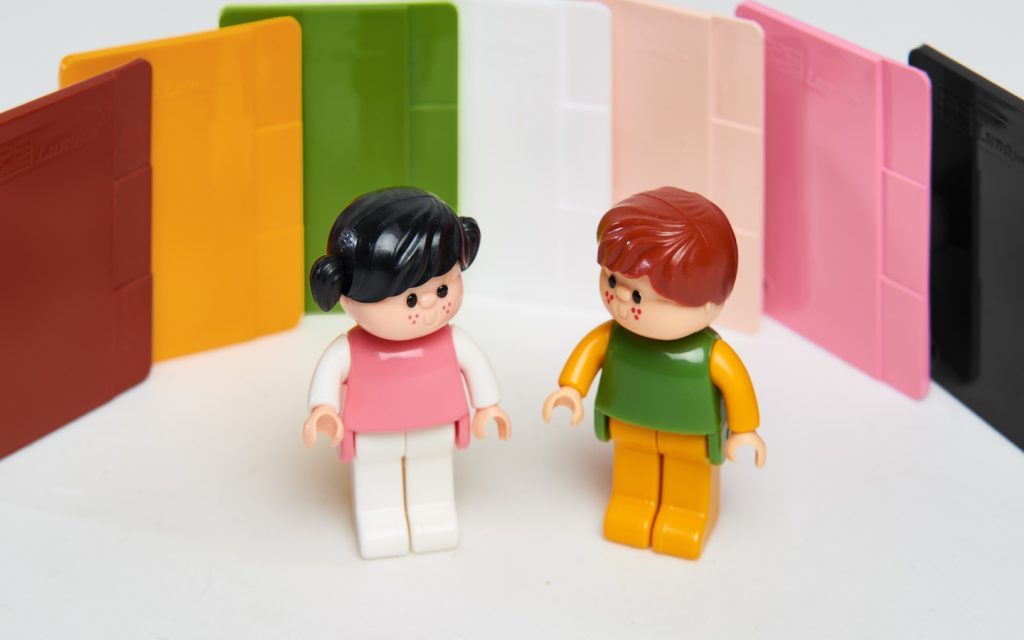
Injection Molding
Injection molding of polymers is a widely used manufacturing process for producing plastic parts in large volumes. It involves injecting molten polymer material into a mold cavity, where it cools and solidifies to form the desired shape. This process is highly efficient, repeatable, and capable of producing complex geometries with high precision.
Advantages of Injection Molding:
- High Production Rates: Suitable for mass production of parts.
- Precision and Consistency: Produces parts with tight tolerances and repeatable quality.
- Complex Geometries: Capable of creating intricate shapes and fine details.
- Material Variety: Works with a wide range of thermoplastic and thermosetting polymers.
Common Polymers Used in Injection Molding:
- Polyethylene (PE)
- Polypropylene (PP)
- Polystyrene (PS)
- Acrylonitrile Butadiene Styrene (ABS)
- Polycarbonate (PC)
- Polyamide (Nylon)
Applications of Injection Molding:
- Consumer Products: Toys, containers, household items.
- Automotive: Dashboards, bumpers, interior trim.
- Medical: Syringes, surgical instruments, device housings.
- Electronics: Connectors, housings, insulators.
- Packaging: Bottle caps, closures, and lids.