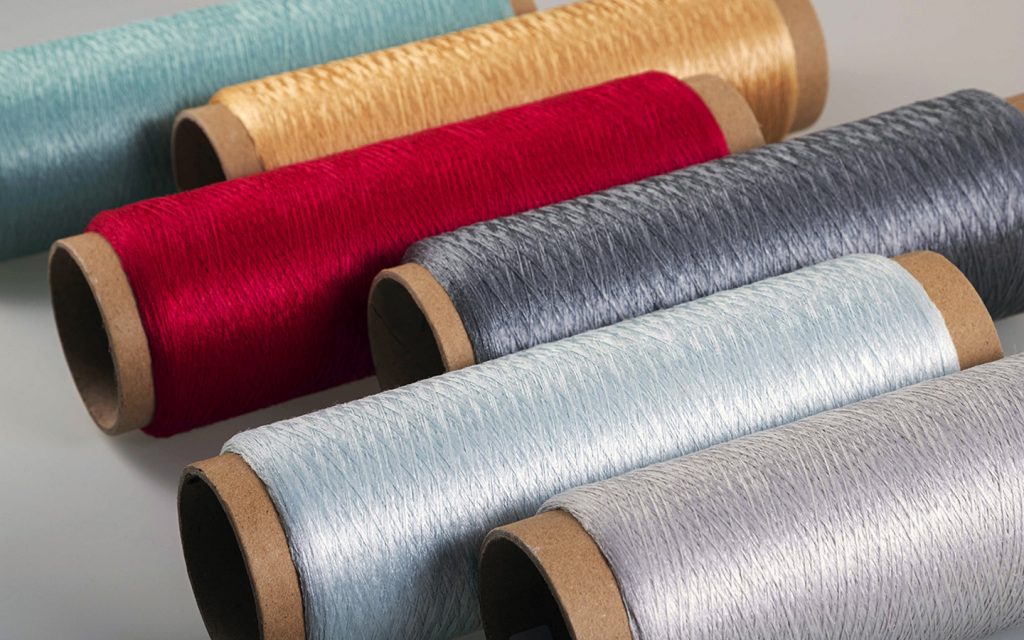
Melt Spinning
The melt spinning process melts polymer with heat until it reaches the correct viscosity for spinneret extrusion. As the name indicates, the chips of fibers are melted and extruded through the spinneret to obtain the fibers. It is used for the polymers not decomposed or degraded by temperatures necessary for extrusion to be melted and pumped through a spinneret in an air chamber. The extruded stream cools and solidifies into continuous filaments and is then drawn out of the chamber, twisted and/or processed further, and subsequently wound onto spools. This spinning process works for making polyamide, polyethylene terephthalate, and polypropylene fibers—common materials in many textiles.
Continuous Filaments
In polymers, a continuous filament refers to a long, unbroken strand of fiber that is extruded from a polymer material. These filaments are typically produced through processes like melt spinning, where the polymer is melted and then forced through a spinneret to form continuous fibers.
Key Characteristics:
– Length: Continuous filaments are essentially infinite in length compared to staple fibers, which are short and discrete.
– Strength: They generally have higher tensile strength and durability due to their uninterrupted structure.
– Smoothness: The surface of continuous filaments is usually smooth, making them ideal for applications requiring fine textures.
– Uniformity: They offer consistent diameter and properties along their length.